A Bit More About Repair - How About Automation?
- Ned Patton
- Jun 5, 2023
- 4 min read
Updated: Jun 13, 2023

Fully Automated Portable Digital Repair (Composites World Jan 20, 2022)
One of the more interesting stories is about the evolution in aircraft repair from manual inspection (tap test) with manual removal and manual scarfing of a defect to automated inspection, material removal, and scarfing. That is what the machine in the pic above is able to accomplish. Developed by American GFM (AGFM in Chesapeake Virginia) the device shown above is called the Portable Scarfing / Composite Repair System or PS/CRS. This device, once it is fully developed, will be a portable, automated composites repair machine that can be placed on an aircraft wing or fuselage surface over the damaged spot and the PS/CRS automatically inspects the surface, finds the extent of the damage, removes the damage to expose good material, makes the scarf patch required to make the repair, and adheres and cures the patch.
Previously, AGFM developed a DoD-funded inspection and repair preparation cell (IRPC) and demonstrated it on a C-130 radome. This IRPC cell performs the inspection using an AGFM multiple axis machine tool, then changes out the inspection tool for a device to mill away the damaged material, and then with another change of tools applies the patch to complete the repair. So, effectively what AGFM has already been able to demonstrate using their already developed machine tools are all of the things necessary to create their PS/CRS system.
And this is just the beginning of the story. There is a robot that Lufthansa Technik has
developed that can scan and automatically repair the skin of an aircraft. This one has already been developed and is certified to repair damage to composite transport aircraft.

Lufthansa Technik Repair Robot (Robotics and Automation Oct. 11, 2017)
This robot is part of the CAIRE project at Lufthansa Technik – Composite Acceptable Inspection and Repair – which is a European aviation project (Airbus is a member) aimed at reducing the time and manual effort required to repair damage to composite aircraft. Previously, composite aircraft like the Airbus A350 and Boeing 787 had to be taken to a certified repair facility for any repairs to the composite fuselage or wings. The robotic machine pictured above does a robotic inspection of the suspected site of the damage, arrange for a scarf patch to be created, mills away the damaged area, and attaches and cures the patch, just like the device shown earlier in this post. This robot, much like the IRPC that was demonstrated by AGFM has to change out tools for each major step of the process.
The two previous examples were all about repairing composite aircraft, but what about the industrial and renewable energy sectors? Well, as usual, I’m going to talk a little bit about wind turbines again. Yes, windmills again, probably because I love the things so much, and was involved very early in the wind turbine industry when I was a grad student at Oregon State.
Wind turbine blades probably suffer more wear and damage than any other composite structure. They are always exposed to whatever the weather throws at them quite unlike aircraft that tend not to take off or land in heavy weather. Wind turbines have to withstand not only wind and rain, they also see hail storms, dust storms, dirt and rocks thrown at them from the wind, lightning strikes, you name it. They are constantly exposed to whatever mother nature can throw at them. The major sources of wear are on leading edges because the leading edge of each blade sees the impact of hail, dust, and anything else that the wind can throw at it. Take for example the San Gorgonio Pass wind farm in the Coachella Valley of California. There are literally hundreds of wind turbines in that wind farm, and that pass is basically an opening in a mountain range in the California desert near Palm Springs that the wind howls through daily. The sandy dust that gets kicked up by those winds causes real havoc on leading edges, wearing them down as if there was sandpaper grinding away at them. The problem is that taking down blades to repair them is a very dangerous job, because human beings have to go up to the nacelle where the blades are attached and detach them so that they can be brought down to be serviced.
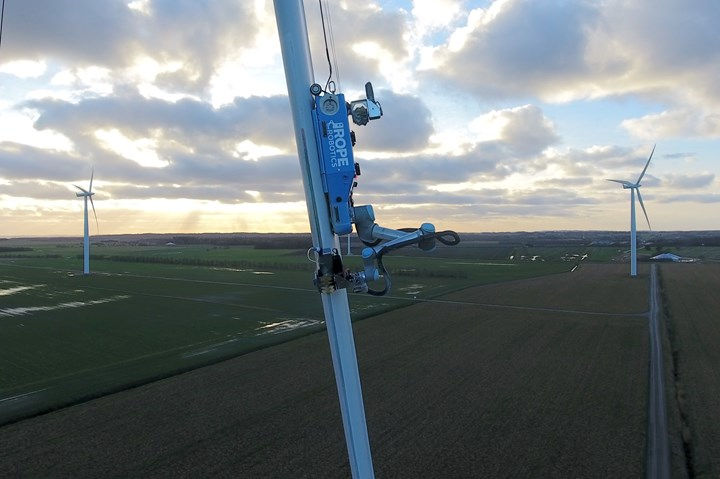
Rope Robotics Automated Wind Turbine Blade Maintenance Robot
(Composites World 6/2/2023)
Fortunately, there are a few new devices that have been developed to perform automated wind turbine blade repair. Rope Robotics (Aarhus, Denmark) has recently demonstrated a positive return on investment for their automated wind turbine blade maintenance and repair device pictured above. After blade damage has been detected by drone inspection, this device is hoisted up to the nacelle with the damaged blade fixed in the vertical down position, and it climbs out on the blade, inspects and makes the repair, and then gets back off of the wind turbine so that it can be put back into service.
And there are other companies, such as Vestas that has their wireless, automated BladeRobot system. Aeromes, a wind turbine maintenance service provider has their robot for performing inspections and repairs. Hitachi Power Solutions has implemented AI-enabled drones to detect damage due to lightning strikes on wind turbine blades in Japan. And finally, Mistras Group has developed what they call a “remote rotor blade monitor” system that detects and tracks damage to wind turbine blades in real time.
All of the systems and technologies that I have talked about in this post have been developed just in the last 10 years, and some of them are still on the drawing board or in development. But, the bottom line is that automated composite inspection and repair is very soon going to overtake the traditional, manual inspection and repair process in the industries that need these services.
So, again, composites have become completely mainstream, and we are even seeing automated inspection, repair, and even structural life monitoring becoming not only commonplace, but required because quite a bit of our composite material infrastructure is aging enough that automated repair to keep things in service longer makes sense.
That’s about it for this week, hope you enjoyed reading this post. And, as for my book - https://mcfarlandbooks.com/product/The-String-and-Glue-of-Our-World/, my publisher tells me that the book will be out in print most likely in August of this year. So, it isn’t that far off.
See you next week.
Comentários