Composites in Ocean Applications – Not as Easy as it Sounds
- Ned Patton
- Jan 17, 2024
- 5 min read
#composites, #fibers, #resins, #marine, #seawater_exposure, #deep_ocean, #UUV, #USV, #sailboat_race, #fast_boats, #sailboat, #power_boat, #ocean
Now you all get to see one of my other great passions – sailing and sailboats. I have owned a number of them over the years, from day sailors to bay sailors. So, I thought I might start off with this pic of a composite hulled three masted square rigger moored in the marine in Gdynia, Poland on the Baltic Coast. Beautiful lines to the hull of this thing.

However, since this is a newsletter about composites, I wanted to get right to it and talk about the use of composites in marine applications. And I am talking here about both things that float on the surface as well as things that dive deep into the ocean.
The material requirements for things like boats that stay on the surface of the ocean – at least that’s the original plan – are somewhat different than the requirements for things that go deep in the ocean. To start with, no matter whether or not the vehicle or other thing is a surface vehicle or an underwater vehicle, the one thing that matters most is buoyancy. In other words, the weight of the water that gets displaced by the boat or submarine must either be equal to the weight of the underwater vehicle or much more than the weight of the surface craft. This is what is called “Archimedes Principle” because it was the ancient Greek mathematician, engineer, astronomer, and inventor Archimedes that came up with this idea and proved it both by math and by making things that floated or sank.
And it is this principle that makes composite materials the material of choice for all manner of water craft, both those that go around on the surface and those that explore the depths.

Especially in the case of the submerged vehicle, the structure that holds all of the equipment inside of it has to be minimum weight because you always want to put more stuff in your underwater vehicle. And to make these things neutrally buoyant (weigh what the water they displace weighs) shaving off pounds, or ounces in the case of things like a small racing sailboat like a laser (pic to the left), is the art and craft of boat and underwater vehicle design.
As you may have guessed, carbon fiber, now that prices have come down as much as they have, is becoming the fiber of choice for high end water craft of all types. It has become something of an obvious choice primarily because of the price, availability, and the newer,
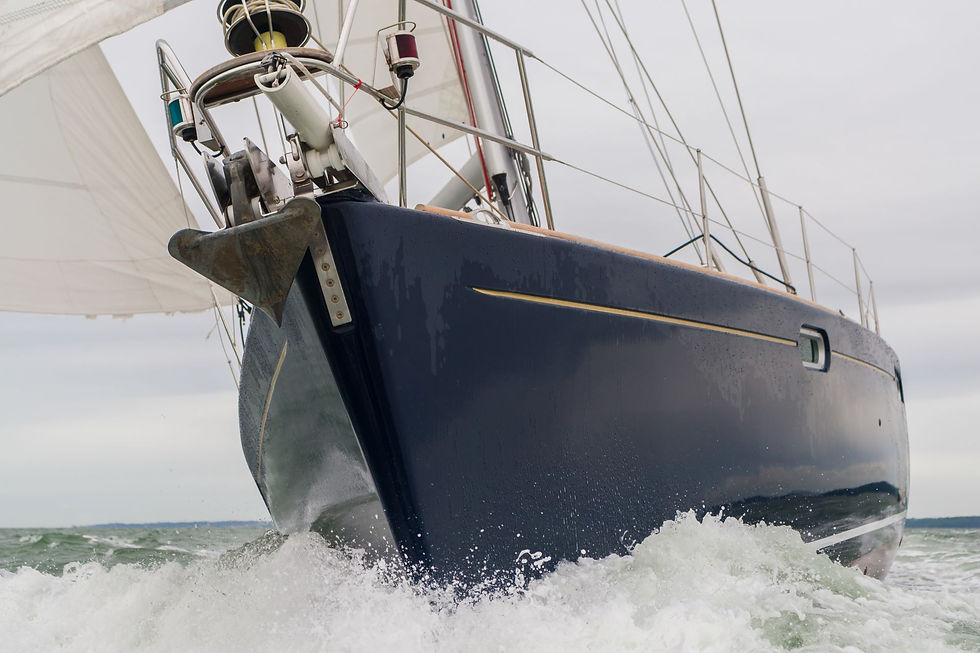
less expensive (less touch labor) means of making things out of composites, including carbon fiber. In addition to this, what are called the “sizings” that are coated on the outside surface of carbon fiber as well as the broad range of product forms for raw material like prepreg fabrics and sheet molding compound have made it much easier to work with and make things out of.
The question then becomes what sorts of things do the designers of these high end water craft have to deal with, just because they are to be used in the ocean. One of the things that is known in the industry and that will always need to be taken into account is that the resins that are used all take up a small amount of water. And most of them, epoxies included, also take up and react somewhat to the salt in seawater. Epoxies aren’t quite as bad in this regard as polyesters, but they do soften up a little bit from long term exposure to seawater.
What this softening of the resin does is to reduce the strength and stiffness of the composite, making the designer use more material in some areas to counteract the softening of the resin. And that adds to weight, so there is a somewhat delicate balance that needs to be understood by the designer of any composite material watercraft. In other words, it is best left to experts.
One of the other requirements always for water craft, whether they are pleasure boats or deep diving submersibles built by the Navy or for oceanographic research, is the overall cost of the vehicle. Exploring the depths is particularly expensive since the deep ocean is the harshest environment on the planet. Carbon fiber / epoxy has become the material system of choice for submersibles of all types, but not necessarily high performance aerospace composites. Minimizing weight is important, but since the structure and hull of underwater vehicles uses significantly more material for the size of the vehicle than do airplanes, cost becomes a much higher priority to minimize than is the case for aircraft. And since composites traditionally are touch labor intensive, oftentimes this cost is dominated by the touch labor required to make the vehicle structure.
This is caused by a couple of factors. First, the total volume of production of any marine vehicle, unless it is your typical 20’ runabout ski boat, is usually in the tens to possibly a couple of hundred of the same design out of the same molds. In the case of underwater vehicles this is especially true, and having more than 10 of the same design made is unusual. So, the economies of scale don’t necessarily work in this industry. This is changing rapidly, but at present to bring one of these vehicles to higher rate production is a fairly expensive proposition. It will of course happen, in the same way that the unmanned aerial vehicle (UAV) market has recently exploded. Within a decade or so the USV and UUV markets will follow and there will be the opportunity take advantage of a larger market to begin to tap into the economy of scale to reduce cost. When this happens the market will take off and you will be able to go down to your local West Marine and buy your own autonomous submersible to go explore the bottom of the ocean.
And, as this happens, newer product forms using more carbon fiber to make for less touch labor and new formulations of epoxies that take up less water and are less susceptible to salt will begin to be seen in the marketplace for raw materials. It really will be the start of a new market segment for composite materials.
That’s about it for this week. But before I sign off I want to make a brief statement about a subject that is on the tip of everyone’s tongue, especially in what I do every week which is to write a newsletter – the use of AI to write blogs or newsletters like this one. While LinkedIn keeps reminding me that all I have to do is to pay them and their AI engine will write my blog for me, I need to let everyone know that either I am old school or maybe just more interested in a much more direct means of communication with everyone, I am not going to use the new AI authoring tools. I am going to use my fingers and my brain to bring these to you every week.
Finally, I need to remind everyone that my book is ready for anyone to purchase. The best place to get one is to go to my website and buy one. I will send you a signed copy for the same price you would get charged on Amazon, except that I charge $8 shipping. Anyway, here’s the link to get your signed copy: https://www.nedpatton.com/product-page/the-string-and-glue-of-our-world-signed-copy. And as usual, here’s a picture of the book for everyone to see what the front and back cover look like.

Comments