Hodgepodge of Recycled and Renewable Composites Applications
- Ned Patton
- 13 hours ago
- 7 min read
This week is going to be sort of a hodgepodge of recycled composite applications and the use of recyclable and renewable materials. I’m doing this because from what I have seen in the composites and materials news feeds that I have been getting lately there are some new and some solid potential high volume applications of recycled, recyclable, and renewable (think plant-based here) materials and precursors to those materials that are finding themselves turned back into composite parts for fairly highly regulated industries.

The first thing I want to highlight here is the use of recycled carbon fiber to make the wing skins of an Unmanned Aerial Vehicle concept demonstrator for the urban air mobility market. This market is replete with demonstrators and even vehicles that are beginning to get close to certification for use as unmanned air taxies. This market is going to explode once several manufacturers get past the required certifications and governments also develop the urban air traffic control systems that will apply to these small airborne vehicles that fly at low altitudes.
That is one of the reasons I picked the lead image for this week’s post. This is a concept image of an electric UAV concept that is being built by the Advanced Materials division of James Cropper PLC (a UK materials company) and the Advanced Materials Research Center which is part of the Technology Innovation Institute of the UAE.
What is demonstrated in this image is the potential for use of recycled carbon fiber in a non-woven product form for primary structure in an air vehicle that will eventually need to become certified to carry humans from place to place in an urban setting – as in air taxis. It these folks are able to pull this off, this will be a great step forward in the efforts to get us to a carbon neutral economy. Fortunately, they have a pretty good chance of doing so because they are in Europe where there is a significant push to do these sorts of things,
In another example from the transportation sector, the automotive industry has been adopting both recycled and plant-based composites now for a few years. One example of this is in the image below where Bcomp and Kia (a division of Hyundai) have developed some key parts for the interior of the new Kia Concept EV2 electric vehicle using Bcomp’s plant-based fibers (flax) in a polyethylene thermoplastic matrix.

This is a good demonstration of the use of inherently recyclable and bio-based composites being used in a mass market automobile. The EV2 is the Kia entrant to the burgeoning mass market small commuter electric vehicle space. These mini-SUVs are intended to compete directly with the Chinese vehicles made by BYD, so they are taking the leading competition in this space head on.
This is just one example of very many automotive manufacturers making use of not only biocomposites in the form of natural fibers and plant based resins, but also recycled plastics and recycled thermoplastic composites for fairly major parts.
In a European example, Volkswagen has apparently been at this for several years at this point. There is a 2019 article in Composites World (Bio-composites break into structural automotive applications, Composites World 1/7/2019) that shows a plant-based polyamide chopped glass fiber reinforced crankshaft cover for their 4 cylinder diesel engine. The polyamide is entirely plant-based, and the chopped glass can come from any source. Since this is Volkswagen, one could easily see that they may be using the glass fiber from companies like Composite Recycling, making this crankshaft cover completely sustainable.
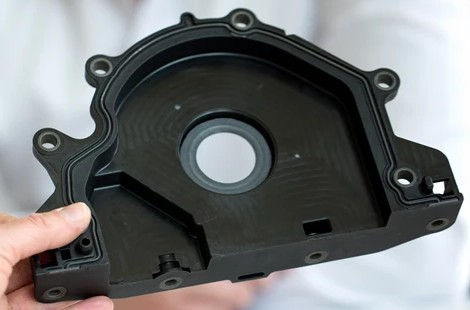
Changing from the metal equivalent of this part to the inherently recyclable plant-based glass reinforced thermoplastic part resulted in a weight savings of 40%. This cover as well as other parts for mass market vehicles has lowered VWs carbon footprint substantially. The resin that was used in this part is from DSM Engineered Plastics in The Netherlands and is made with a 70% castor bean oil polyamide they call EcoPAXX PA 410.
This is just a demonstration of VWs push to be carbon neutral as soon as possible in all of their vehicles and manufacturing operations. In fact, one of their newest entrants to the market is the return of the iconic VW T1 van, the VW ID Buzz. In a significant nod to the California hippie days of the 1970’s, this is VWs best example of the use of natural fibers, sustainable materials, and recycled materials for a mass market application. The tailgate of ID Buzz is made of a natural fiber reinforced recycled thermoplastic composite that is not only inherently carbon neutral, it is also 100% recyclable. And the interior of the ID Buzz uses a fiber that is made using recycled ocean plastic and recycled PET (polyethylene terephthalate) soda bottles. VW says that it uses 63 recycled PET bottles in every ID Buzz. Recycled plastics are used for seat covers, floor mats, parts of the headliner, underbody panels and several of the other interior plastic panels in the Buzz. That actually makes me feel pretty good about our latest purchase. We got a two tone one in Pomelo Yellow, which is the color that you see in the VW ads targeted at the California market. This is going to be the largest market for this iconic retro VW van. My prediction is that, since VW absolutely nailed it with the ID Buzz, VW will see very good sales for this thing. It went on sale last year in Europe, and has already made quite a stir there.
VW is apparently using the ID Buzz to demonstrate a product that has as much recycled and natural materials as they can in a mass market vehicle. And what VW has developed specifically for this vehicle is now being pushed into all other VW products, so fairly soon this company will be one of the greenest automakers in the world. That is at least their intent, and it appears that they are walking the walk with all of their new products. They have even used a battery in this all electric vehicle that does not use cobalt, which keeps the cost of the battery down as well as not requiring the use of a fairly scarce rare earth element.
Recycled composites are also finding their way into some other high tonnage, regulated applications. Recycled fiberglass composites from wind turbine blades are being remade into new wind turbine blades. Companies like Composite Recycling are providing the raw materials for this as well as the use of recycled wind turbine blades and old boat hulls for new boat hulls. I wrote about the consortium involving Composite Recycling and Beneteau among others a couple of weeks ago, which is just one example of where this is happening at a fairly large scale.
Recycled carbon fiber is even making it into products produced by Boeing and Airbus for the commercial aviation market. Boeing is collaborating with ELG Carbon Fibers to divert as much as a million pounds of composite material a year from 11 of their manufacturing sites to be used in other industries, like automotive and sporting goods. And Boeing is also working on getting more recycled composite content into their newer generation transport aircraft. The image below shows a molded interior sidewall panel for a Boeing aircraft that is made using recycled carbon fiber in a thermoplastic matrix. They collaborated with Cannon Ergos, an Italian company that has been working with Mitsubishi Chemical Advanced Materials to design and build a customized thermal press unit for making these panels at a high rate.
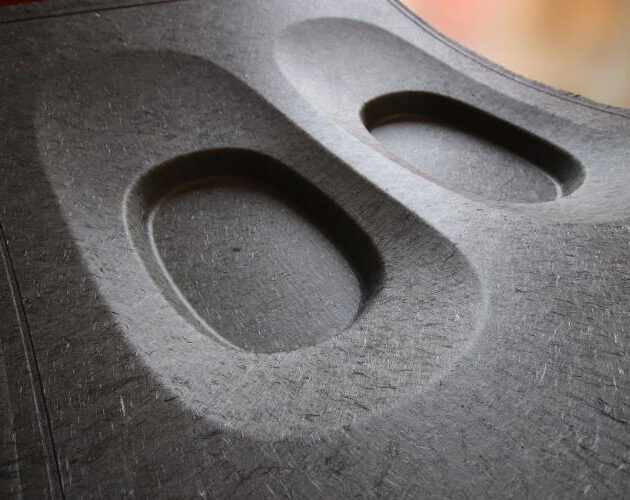
Airbus is also using recycled thermoplastic composites in their NextGen cabin interiors and their new Cargo aircraft concept, where they are incorporating these materials into the fuselage demonstrators for not only their next generation cargo aircraft, but eventually passenger aircraft as well. This of course gives these two aerospace giants more ways to make lighter weight aircraft which makes them more fuel efficient, while also reusing materials that would otherwise end up in landfills. Airbus has even produced a carbon fiber reinforced thermoplastic fuselage demonstrator that is part of their Clean Sky 2 project.

The last example that I’m going to use this week is the development of bio-based composites for another large tonnage, regulated industry. This example is a project from the Aitiip Technology Center in Zaragoza, Spain called CUBIC. This project is funded and is part of the Circular Bio-based Europe Joint Undertaking (CBE-JU), the EU’s program for research and innovation, also called Horizon Europe. The CUBIC project is intended to develop 100% recyclable, bio-based composite materials and manufacturing technologies, initially for two fairly high tonnage, regulated applications – car seats and hydrogen storage pressure vessels. They are going so far as to not only develop material solutions, but also the manufacturing technology to deliver these things at scale. They are working with a broad consortium throughout the EU with representation from industrial partners, EU R&D organizations, and a university to bring bio-composites into the mainstream in Europe. It appears that they have the funding as well as a solid pan-European partnership of the right organizations to be able to make this project a success.
That’s about it for this week. As always, I hope everyone that reads these posts enjoys them as much as I enjoy writing them. I will post this first on my website – www.nedpatton.com – as then on LinkedIn. And if anyone wants to provide comments to this, I welcome them with open arms. Comments, criticisms, etc. are all quite welcome. I really do want to engage in a conversation with all of you about composites because we can learn so much from each other as long as we share our own perspectives.
My second book, which should be out in the fall, is a roadmap to a circular and sustainable business model for the industry which I hope that at least at some level the industry will follow. Only time will tell. Since my publisher and I have finally come to agreement about the title for my next book, our daughter has been kind enough to put together a draft of the cover of the book. I’ve included that at the end of this post as promised. Let me know whether or not you like the cover. Hopefully people will like it enough and will be interested enough in composites sustainability that they will buy it. And of course I hope that they read it and get engaged. We need all the help we can get.
Finally, I still need to plug my first book, so here’s the plug. The book pretty much covers the watershed in composites, starting with a brief history of composites, then introducing the Periodic Table and why Carbon is such an important and interesting element. The book was published and made available last August and is available both on Amazon and from McFarland Books – my publisher. However, the best place to get one is to go to my website and buy one. I will send you a signed copy for the same price you would get charged on Amazon for an unsigned one, except that I have to charge for shipping. Anyway, here’s the link to get your signed copy: https://www.nedpatton.com/product-page/the-string-and-glue-of-our-world-signed-copy. And as usual, here’s a picture of the book.

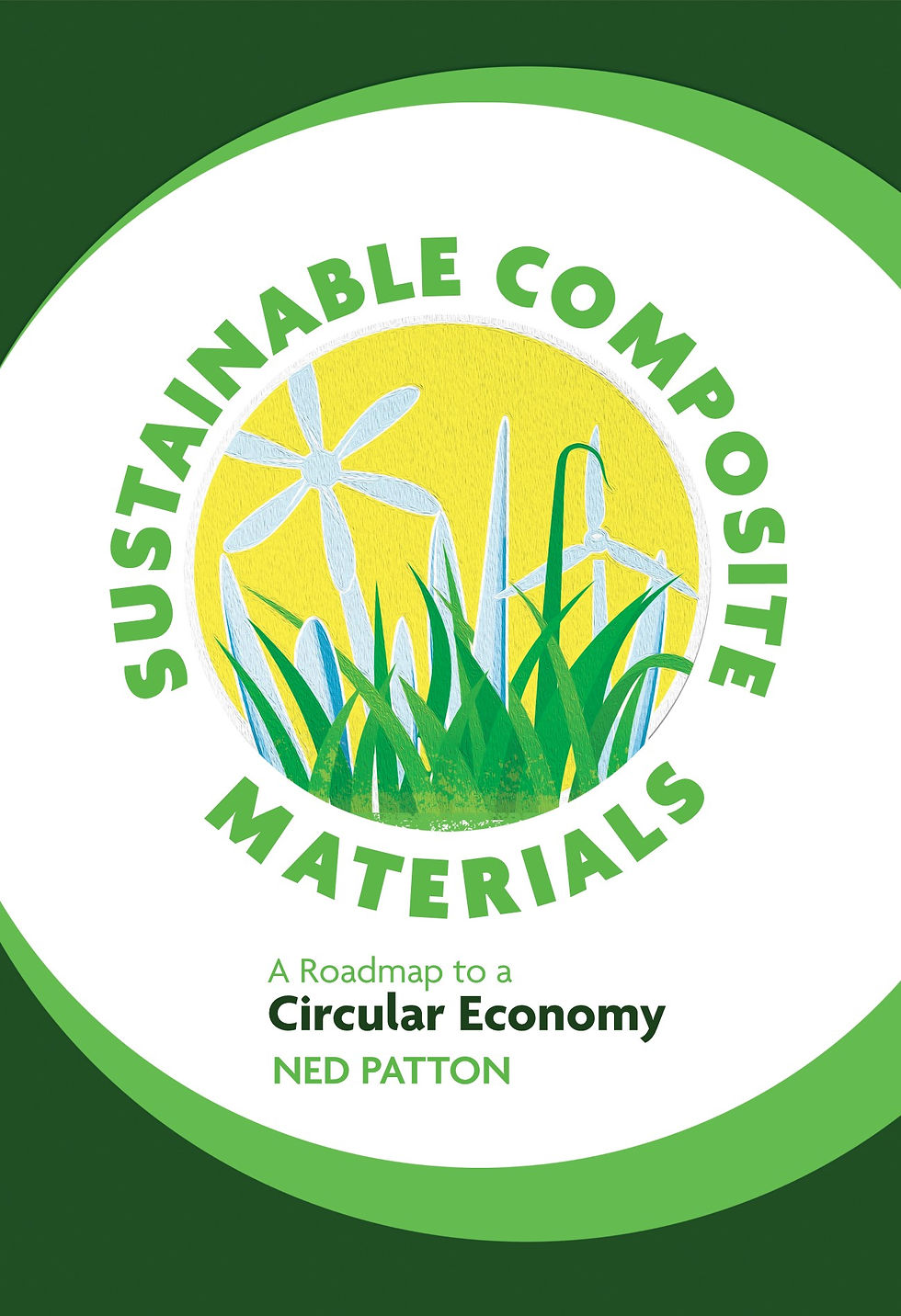
Comments