Part 1 of PFAs and Microplastics - The Chemistry and Process of Making Acrylonitrile
- Ned Patton
- Feb 17
- 8 min read
As promised from last week, this is part 1 of a multi-part series on the impact of the composites industry on the release of forever chemicals (PFAs or per- and polyfluoroalkyl substances) and microplastics into the environment. These two plastics and plastic manufacturing byproducts have gotten significant attention in the media recently and there is a movement that has begun to control and potentially eliminate them from our industrial and commercial processes as well as our homes. This is happening primarily in Europe currently, but the US is not that far away from beginning to take a long look at how these modern day pollutants can be eliminated from our environment.
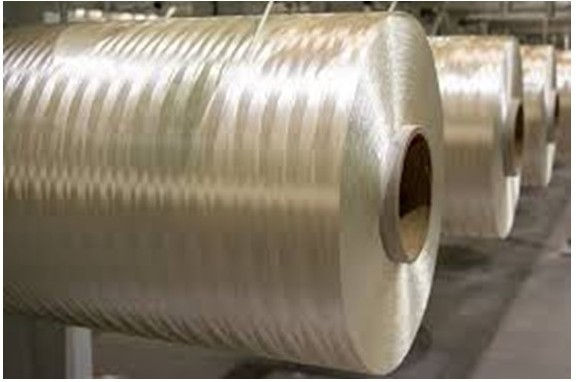
I have used this pic in previous posts because this is one of the good news stories about the development of acrylonitrile and the polyacrylonitrile that is currently the most common precursor to making carbon fibers. This pic is from a Composites World article where they are talking about plant-based sources of acrylonitrile that eliminate all of the toxic chemistry and environmental damage caused by the refining of petroleum into the propene and other chemistries necessary to make acrylonitrile.
While I have discussed the manufacture of acrylonitrile by conventional means in previous posts (and in my upcoming book) I thought with this post I would delve a little deeper into the chemistry for making acrylonitrile from refined petroleum products.
There are a few processes that have been used to make acrylonitrile traditionally. The most prevalent one is what is called the “Sohio” process. It was developed in the 1950’s at Standard Oil of Ohio – hence the name. The process starts with propylene, which is sourced primarily from the same petroleum cracking process that is used to make gasoline and diesel fuel. This is of course done in some of the large oil refineries both here and in the EU, India, China, even in Africa and South America. When you “crack” the heavier (longer hydrocarbon chain) petroleum products down into shorter chain hydrocarbons you get this mix of different hydrocarbons all of which are shorter chain. Propane is one of the gases that is given off in this process, along with a mix of different hydrocarbons. From that mixture propene (or propylene) can be derived by running this mix over a catalyst bed to strip off some of the hydrogen to produce things like propene. Along with this most commonly also you get ethylene, hydrogen gas, and some other compounds from which you can distill out the propene. The cracking process is typically done in the tall distillation towers that you see in every oil refinery.
Once the propene is ready to use, to make acrylonitrile using the Sohio process, propene, ammonia, and air are run through a powdered catalyst in a fluidized bed to produce acrylonitrile, acetonitrile, hydrogen cyanide, and ammonium sulfate. Then the acrylonitrile and acetonitrile are distilled off in another distillation process and the ammonium sulfate (white powdery substance) and hydrogen cyanide gas are collected and removed. In the past, when they were first making this stuff, the hydrogen cyanide was vented to the atmosphere. It was judged at the time that as long as they did not release too much of this extremely poisonous gas into the atmosphere it would mix down to a concentration low enough to be safe. And since it is an acid and will react with moisture in the atmosphere, it was thought at the time that it would decompose before it could do any real harm. Fortunately things have changed and this gas is no longer released to the atmosphere. It is instead collected and stored for use in some other organic processes for making other plastics.
There is another, older process for making acrylonitrile that is not used as much as the Sohio process but is still in use in some plants today. In this process, hydrogen cyanide is reacted with acetylene over a catalyst bed that is typically a copper chloride salt. This process has been largely overtaken by the Sohio process because it is more expensive and less efficient (lower yields) than the Sohio process. And this acrylonitrile is not normally used in making carbon fiber. Rather, it is more integrated into older production processes for making ABS and styrene-based plastics. Basically, HCN and acetylene come in one end of the process and either ABS or other styrene based plastics come out the other end with acrylonitrile being just an intermediate step in the plastic production process rather than being the end product. And, since this is a composites newsletter, I am just mentioning it here for completeness.
The world’s largest producer of acrylonitrile is a large Belgian petrochemical company named INEOS. This company has a very long history and has made a number of acquisitions along the way. What became INEOS was formed in the UK in 1890 as an alkali company making Caustic Soda (sodium hydroxide) for use industrially in the UK. About 5 years later, a German company started making formaldehyde. Then in the early 1900’s a UK refinery and a French refinery started up. The French refinery started a petrochemical company in 1949, then created a naphtha cracker a few years later, and the German refinery started up a phenol/acetone plane a year later. Then the acquisitions started with Bayer, BP, Amoco, Union Carbide in the US, and the story continues with companies eventually ending up on the Amsterdam Stock Exchange, and by 1998 INEOS was formed out of this conglomeration of oil and gas and petrochemicals businesses. This is one of the typical stories in the composites business where the major players are relatively new and are quite commonly made up of pieces and parts of storied older companies, most of which have gone back to their core businesses and left this rather volatile (sorry about the pun here) market to a large conglomerate.
The bottom line to this story, at least the propene precursor type of acrylonitrile production, is that there is some quite toxic chemistry involved in its production. There is good news, however. INEOS has fairly recently inked a deal to use plant-based glycerol from Trillium for making acrylonitrile.
This is one of the other acrylonitrile production processes that I want to talk about in this post, primarily because the chemistry is much less toxic, does not produce toxic byproducts, and uses a plant-based precursor rather than all of the toxic chemistry and effluents that come from the refining and cracking of petroleum. I need to provide a couple of molecular diagrams here to explain what I’m trying to get at.
First – acrylonitrile from propene:

Now - acrylonitrile from acetylene:

What is not shown in either of these two graphics are all of the intermediary chemistries and by-products that are produced in each process. While the propene to acrylonitrile process looks on paper to be nearly as simple as using glycerol to start with, in a reactor it is actually a single step process that produces a mixture of a number of different chemicals. Water is produced, as well as acrylonitrile, acetonitrile, and hydrogen cyanide. And to make this be a one step process, more ammonia is used than is necessary which is reacted with sulfuric acid to produce ammonium sulfate. The ammonium sulfate can be used as fertilizer, but the other compounds all have to be captured, separated, and put into separate product streams.
Two other issues with this process are that it has a fairly low yield for a petrochemical process, and it is highly exothermic – it produces a lot of heat. Since exothermic reactions can run out of control if not very tightly controlled, this process does require very stringent temperature control. Both of these make the process of manufacturing acrylonitrile from propene relatively expensive. This is the reason there are only a very few manufacturers of acrylonitrile using the Sohio process, with INEOS being the largest one.
Making acrylonitrile using glycerol as a precursor gets around a number of these issues, especially the sourcing of the starting materials. As it turns out, some smart chemists at Southern Research developed a plant sugar based acrylonitrile production process using glycerol which is a byproduct of the paper making process and can be extracted easily from both forest products and agricultural waste. Glycerol is merely the alcohol of the common sugar glucose and is usually made through hydrolysis of glucose.
There is another interesting pathway to this same result using biological fermentation of other plant sugars. In a 2017 project at the National Renewable Energy Laboratory (NREL) in partnership with ORNL, the University of Colorado Boulder, the Colorado School of mines, and the Mid-Atlantic Technology, Research and Innovation Center they used sugars extracted from non-food waste in a bioreactor to produce 3-hydroxyproprionic acid. From this, they used the same sort of chemistry that Southern Research used to produce Bio-ACN. So, this is another pathway to the same result, only using biological fermentation of the plant waste sugars rather than extraction and hydrolysis.
Since the time that Southern Research developed this process, a company by the name of Trillium Renewable Chemicals licensed this technology, scaled it up to where it can be made industrially, and is marketing it as Bio-ACN. And Trillium just recently inked a deal with INEOS to set up the first full scale production pilot for making Bio-ACN at the INEOS acrylonitrile plant in Port Lavaca, Texas. That line should be up and running this year producing Bio-ACN for the carbon fiber business at scale.
That’s about it for this week. This is part one of this multi-part series on this topic. It follows directly from the subject of my second book on composites sustainability, so I’m treating this as a natural progression of this newsletter.
As always, I hope everyone that reads these posts enjoys them as much as I enjoy writing them. I will post this first on my website – www.nedpatton.com – as then on LinkedIn. And if anyone wants to provide comments to this, I welcome them with open arms. Comments, criticisms, etc. are all quite welcome. I really do want to engage in a conversation with all of you about composites because we can learn so much from each other as long as we share our own perspectives.
My second book is now completely in the hands of my publisher. Most of you know that it is about what I have been writing in these newsletters for the last 6 months or so – sustainability of composites and a path to the future that does not include using fossil fuels for either the raw materials or the process energy to make composites. The title of the book, at least for now, is “Close the Circle, A Roadmap to Composite Materials Sustainability.” It truly is a roadmap which I hope that at least at some level the industry will follow. Only time will tell.
Finally, I still need to plug my first book, so here’s the plug. The book pretty much covers the watershed in composites, starting with a brief history of composites, then introducing the Periodic Table and why Carbon is such an important and interesting element. The book was published and made available last August and is available both on Amazon and from McFarland Books – my publisher. However, the best place to get one is to go to my website and buy one. I will send you a signed copy for the same price you would get charged on Amazon for an unsigned one, except that I have to charge for shipping. Anyway, here’s the link to get your signed copy: https://www.nedpatton.com/product-page/the-string-and-glue-of-our-world-signed-copy. And as usual, here’s a picture of the book.

Comments