I heard about this a few days before it was announced at JEC World in Paris. There is some very good and interesting news in the fiberglass recycling and reuse frontier. I need to talk about this news and also bring everyone up to speed on just where all the rest of the fiberglass and composite recyclers stand and what is being done with the recycled materials that begin to make pleasure boat hulls and wind turbine blades truly circular.
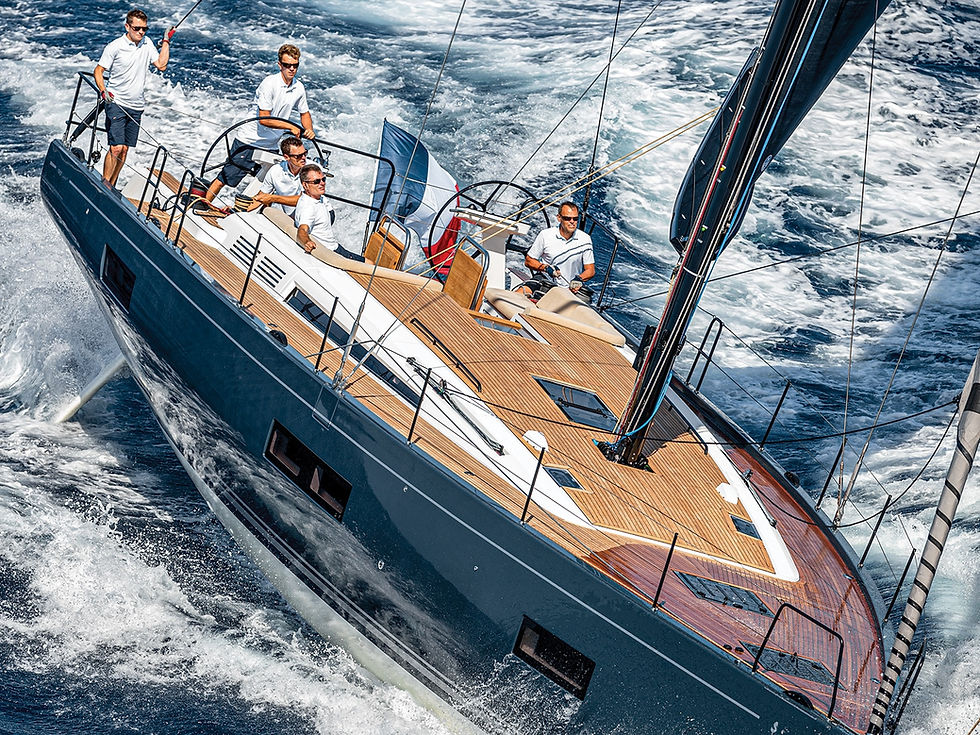
The picture I’m leading off with here is from one of the world’s leading large sailboat manufacturers, Beneteau. Headquartered on the North Atlantic coast of France in what was in 1884 a little fishing village, Croix-de-Vie, they have been in the business of building fishing boats, pleasure boats and cruising and racing yachts for 130 years. This boat is their “First Yacht 53” – a 53’ single masted sloop that is in the classic Beneteau style with a flush rear deck and the two piloting stations. This is one of Beneteau’s original innovations and they have kept this in every boat over 30 feet (10 meters) they have made. The Beneteau Oceanis series of yachts has been one of the most successful open ocean cruising boat series ever made. And, while other large boat manufacturers have come and gone, the classic styling, performance, and seaworthiness of Beneteau yachts has allowed them to stay in business as long as they have. It doesn’t hurt that Beneteau is still a family owned and run company.
So, now that we have established the reputation of Beneteau in the sailing yacht world, I need to let everyone know about the announcement that was made at JEC World a week or so ago. I have written about all of the companies that I mention here in past posts and their innovative means of recycling used wind turbine blades and being able to save the glass fiber in a form that it can be directly reused in new composite structures, while also retaining the resin as an oily recyclate that can be very easily turned back into new polyester or vinyl ester resins for use with the same glass fiber that came from the wind turbine blades.
What was announced is a consortium of companies, each of which are leaders in their market segments, and who together have come up with a revolutionary way to build sailing yachts. The companies are:
Groupe Beneteau, the world’s leading manufacturer of sailing and motor yachts
Veolia, global leader in waste management and environmental services
Composite Recycling, one of the pioneers in recycling composite waste
Arkema, a world player in specialty materials with an established series of resins made using recycled plastics, including their Elium® recyclable resin system
Owens Corning, the company that invented glass fiber and one of the largest and most respected names in the business, especially for their innovative mindset and new product development.
Chomarat, a European specialist in technical textiles (structural and other) and composite reinforcement
This group of companies has banded together to develop their products to the point where Beneteau Groupe will be able to make their sailboat hulls out of recycled materials. The plan is for Veolia to use their already developed logistics chain to bring composite scrap to a site where Composite Recycling can use the technology developed by Fiberloop to recycle used wind turbine blades into usable glass fiber mats and thermolysis oil. The resultant recycled fiber will be sent to Owens-Corning for remanufacturing into glass fiber ready to be woven into the appropriate textiles for boat manufacturing by Chomarat. The thermolysis oil will be delivered to a plant that Arkema sets up to turn it into new Elium® resin. Then Groupe Beneteau will take the recycled and reprocessed glass fiber in a form suitable for boat manufacture and the Elium® resin from Arkema to manufacture new sailboat and motorboat hulls.
This is the first instance of completely closing the circle in composites that I have seen to date. And the really ground-breaking thing about this is that not only does it enable completely sustainable boat building using recycled materials, the boat hulls at the end of their life can be recycled again into glass fiber and resin and made into new boats.
Finally, since this is a consortium of several companies that are each interested in demonstrating a sustainable future for their part of the business and have also decided to work collaboratively to demonstrate a circular model for composite materials, this is a model that can be copied in the composites industry at large.
Just to make this real for everyone, here’s the link to the announcement from JEC World 2025 - https://www.jeccomposites.com/news/spotted-by-jec/industrial-alliance-unveils-circular-model-for-nautical-construction/?news_type=announcement,process-manufacturing&end_use_application=aerospace,automotive-road-transportation,building-civil-engineering,marine-transportation-shipbuilding,renewable-energy&tax_product=glass-fiber&exceptionaltags=sustainability.
This article has a wonderful graphic about this announcement that tells the entire story well.
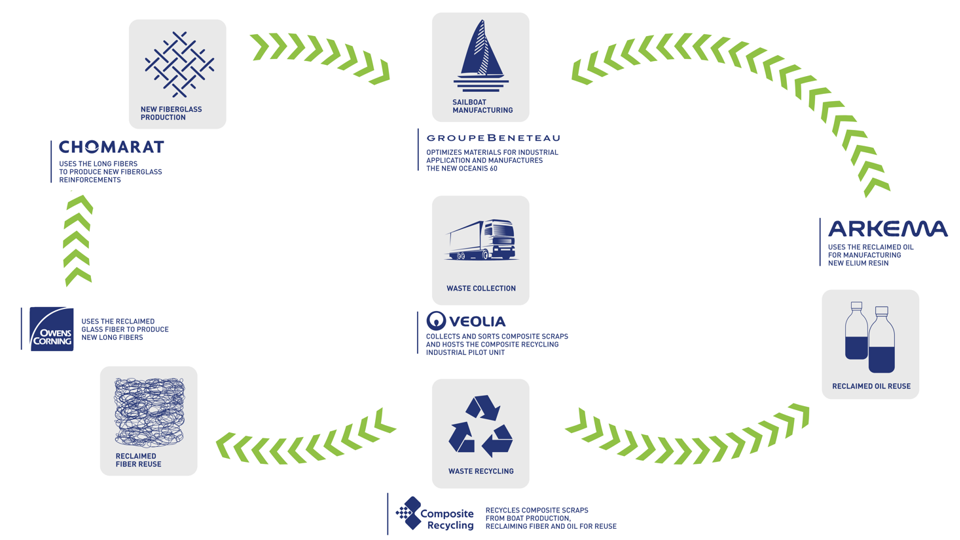
This consortium is going to lead the pack into the future, because the future for composites must be a circular model that is sustainable over the long term. Petroleum and natural gas will at some point become scarce commodities, maybe not in our lifetimes but our children and grandchildren will certainly see oil prices rise steadily as new production of oil and gas begins to be harder to come by because only the marginal wells will be able to produce it. It might take 50 to 100 years, but it will happen. We have to plan for that now and this consortium of major industry players in one of the highest tonnage uses of composite materials is a very good start.
And as promised, there is more good news in end of life composite material recycling. An article in Composites world at the end of December 2024 (https://www.compositesworld.com/articles/trends-fueling-the-composites-recycling-movement), lays out the groundwork for where the composite material recycling business was at the end of last year. That article focused primarily on carbon fiber composites, which is the other side of the business. Carbon fiber composites made using epoxies are somewhat more difficult to deal with than is fiberglass, but the value of the recyclate is much higher as long as the original properties of the carbon fiber are by and large retained in the recycled material. In the mechanically recycled carbon fiber composites arena, there are two companies that are working with composites manufacturers to recycle mostly manufacturing scrap, but also to recycle end of life carbon fiber parts into products that can be turned into new composites for industries like sporting goods, consumer electronics, and mobility or transportation.
One of these companies I have written about in previous posts, Fairmat in Paris. I wrote about them working with Hexcel in Europe and also installing a new carbon fiber scrap recycling facility at Hexcel’s Salt Lake manufacturing plant. Fairmat is also working with Exel Composites, Dassault Aviation, and several other companies in the aerospace composites industry to recycle their scrap into usable products for the same industries that I talked about above. The end result is a product that can come in sheet form or blocks, or even ships that can then be reused or remolded into something useful.
Another company that is working with carbon fiber scrap from Toray is Elevated Materials in Gardena, CA (Los Angeles area). They are working with the Toray facility in Tacoma, WA that is the major carbon fiber composite material supplier to Boeing and all of the Southern California and Puget Sound aerospace businesses. This is just yet another example of how developed this business really is.
There are several other examples cited in the Composites World article of companies that are commercializing a variety of methods for recycling carbon fiber and glass fiber composites of all kinds. In fact, since there is such a large palette of different resin systems used with different fibers, there isn’t one solution that fits every recycling situation. At the lower technological end there are mechanical methods that grind up the composite into small enough pieces that it can be used to reinforce concrete for high rise construction. Other mechanical methods that chop the materials into larger pieces along with things like thermolysis or pyrolysis will retain more of the properties of the fiber and even sometimes the resin. And there are also chemical and solvent based methods that can be used to dissolve the resin away from the fibers, some of which also retain a good bit of the resin for reuse.
The bottom line here is that the industry is beginning to wake up to the reality of their future and now have a very clear understanding of the need to develop circular economies for their materials if they want to be in business 50 to 100 years from now. And it is some of the biggest names in the business that are taking this seriously enough that they are investing real dollars (Euros?) in the technologies needed to become sustainable businesses.
That’s about it for this week. As always, I hope everyone that reads these posts enjoys them as much as I enjoy writing them. I will post this first on my website – www.nedpatton.com – as then on LinkedIn. And if anyone wants to provide comments to this, I welcome them with open arms. Comments, criticisms, etc. are all quite welcome. I really do want to engage in a conversation with all of you about composites because we can learn so much from each other as long as we share our own perspectives.
My second book is now completely in the hands of my publisher. Most of you know that it is about what I have been writing in these newsletters for the last 6 months or so – sustainability of composites and a path to the future that does not include using fossil fuels for either the raw materials or the process energy to make composites. The title of the book, at least for now, is “Close the Circle, A Roadmap to Composite Materials Sustainability.” It truly is a roadmap which I hope that at least at some level the industry will follow. Only time will tell.
Finally, I still need to plug my first book, so here’s the plug. The book pretty much covers the watershed in composites, starting with a brief history of composites, then introducing the Periodic Table and why Carbon is such an important and interesting element. The book was published and made available last August and is available both on Amazon and from McFarland Books – my publisher. However, the best place to get one is to go to my website and buy one. I will send you a signed copy for the same price you would get charged on Amazon for an unsigned one, except that I have to charge for shipping. Anyway, here’s the link to get your signed copy: https://www.nedpatton.com/product-page/the-string-and-glue-of-our-world-signed-copy. And as usual, here’s a picture of the book.
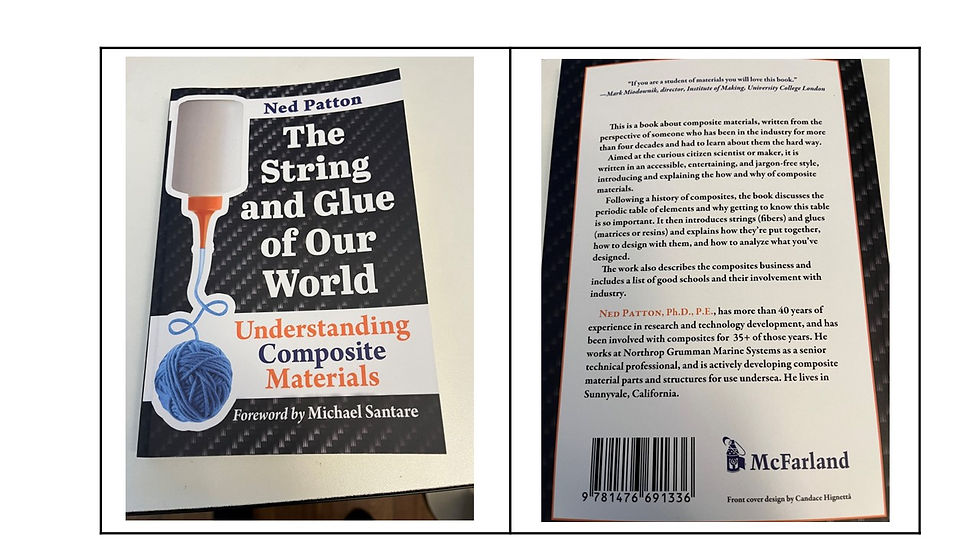
Comments