Use of Composites in our Infrastructure - the First of Many Posts
- Ned Patton
- Apr 23, 2023
- 3 min read
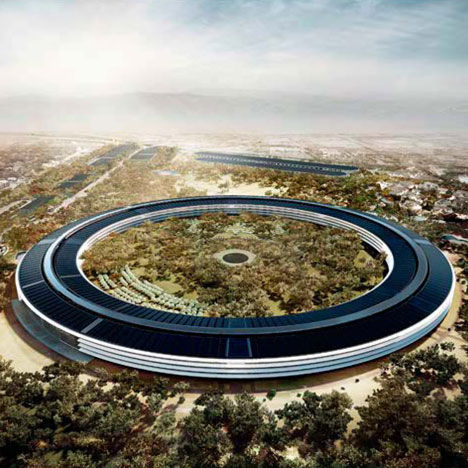
I’m going to write a bit about composites in infrastructure in this group of posts – and there are several of them – because believe me, there’s lots to talk about here. Composite materials are making major inroads into our infrastructure for a number of reasons. They are lighter weight, they don’t corrode, they handle the elements and harsh environments really well (salt on the roads in the Northeast for instance), and the cost of composites has come down to the point where they are cost competitive with steel and even steel reinforced concrete.

A good example is the pic to the right which is a railway station in Czechoslovakia where the entire people platform is made using composite materials. Steel reinforced concrete would have been too heavy, and with the winters in Czechoslovakia would not have lasted nearly as long as the composite material platform will.
With all of this in mind, the business of making large things out of composites has evolved in the last 20 years or so from a niche business to becoming very mainstream. With the increasing application of automated manufacturing equipment and processes, and the development of resins, fibers, molds, preforms, and pre-pregs at large scale that are tailored to these large infrastructure projects, some of these infrastructure projects are even less expensive than building much the same thing using more traditional materials.

Another advantage of composites is the aesthetic value of the nicely curved shapes that you can make easily using composite materials that would be much more difficult to make with steel or aluminum. Take for instance the pic to the left. That is the roof of Medinah Station on the new Saudi Arabian high speed rail network. Those composite panels are actually glued together with the advanced adhesives that are now available and that are specifically tailored to large infrastructure projects like this. And, of course, that roof provides much needed shade for all of the passengers getting on and off of the trains. This is after all in the middle of the Arabian Desert, so it's hot and dry.
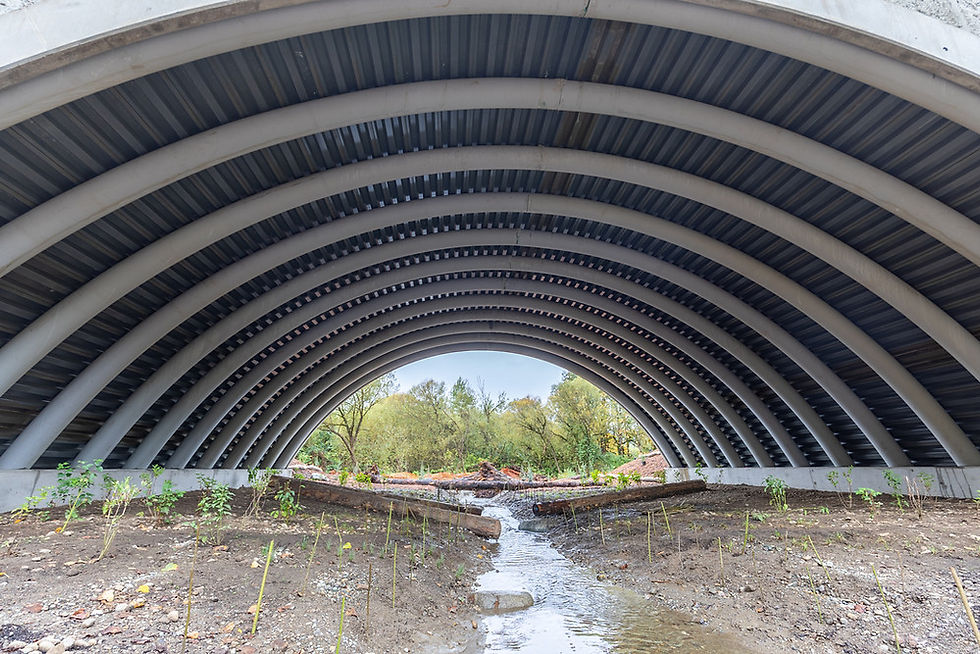
The pic to the right shows a bit more of not only the aesthetic appeal of building something out of composites, but also the strength, stiffness, and light weight that using composites over steel or concrete affords. The bridge in this pic is one of a series of bridges built in the U.S. using a very innovative composite material beam structure. That bridge was built by AIT Bridges who developed this idea of building a bridge over sensitive waterways without disturbing the waterway or the ecosystem around it. The photo below shows a model of that bridge under construction.

To build this bridge, concrete foundation walls are poured at each side of the series of arched composite material tubes, and then a composite material covering is put over the tubes (grey pieces in the photo). Once the tubes are covered, the normal process of putting dirt around the bridge can take place without disturbing the stream bed below. Those white composite material tubes are stronger and stiffer than the steel reinforced concrete that they replace. In addition, all of the materials to make the bridge can be brought to the site on a few trucks, rather than having on the order of 100 concrete trucks come to a remote site to build a bridge.
All of what you see in these pics has happened in the last 15-20 years or so as the costs of the raw materials that make up composites and the cost to fabricate big things out of composites has come down. And this is a trend that will continue into the future for many years to come.
There is lots more to talk about in the infrastructure world, so the remainder of the posts in this "Infrastructure" series, I’m going to focus on some of the innovative and new building materials that have enabled the business of composites in infrastructure to blossom the way it has. I'm also going to provide more examples and talk about some of the newer and more innovative and cost effective fabrication techniques that 10 years ago could only be dreamed about. Stay tuned for more to come.
Comments