I want to delve back into natural fibers and resins a bit this week and bring everyone some of the latest work in this field. It is of course exploding now that there are companies that are

beginning to get these materials into high volume industries like the auto industry. I touched on this some time ago, so the pic attached here won’t surprise anyone. Yes, that’s the front end of a Porsche 718 Cayman. This is actually one of their race versions of this car, and they raced this one in the Nürburgring 24 hour endurance race in September of 2020. This of course saves considerable weight up top, so these cars will handle even better than the 911’s with steel of fiberglass bodies. There have been trial parts like the flax fiber bike frame you see
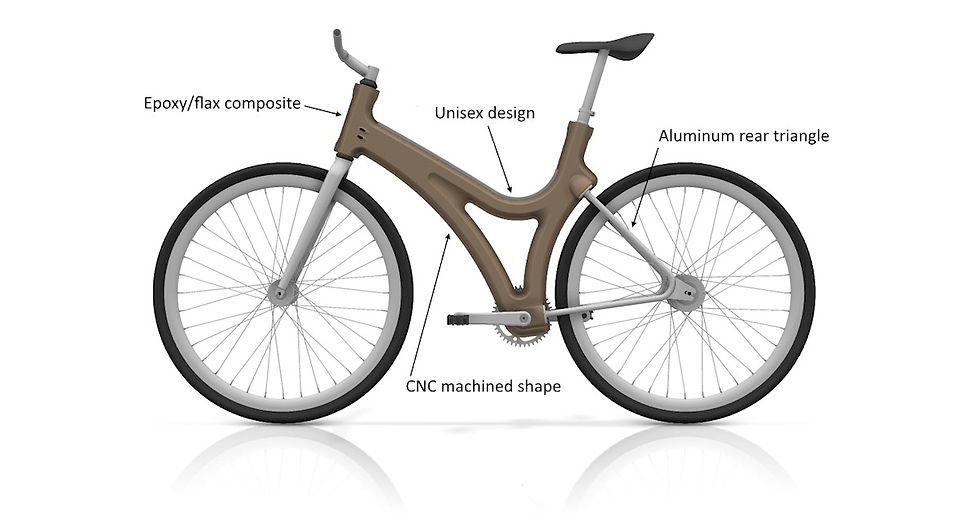
here. There is also considerable adoption of flax fiber composites in things like interior door panels, trunk liners, hood liners, interior door insulation, and even a frame for a sky roof on a Mercedes Class sedan. I touched on this in an earlier post, and the auto industry is using flax fibers in door panels and door panel sound insulation, trunk liners, hood liners, and several other applications. There are several images sprinkled throughout this post that demonstrate the applications of flax fibers in particular to the auto industry. While these

parts are not primary structure, some auto manufacturers – most notably VW/Porsche and Mercedes Benz – have adopted flax fiber interior parts. They have even been used to make a fashion statement, like the pic you see here from Porcher Industries in France. They have developed an entire line of woven flax fibers in a flax fiber compatible thermoplastic.
So why don’t we see some production autos with natural fiber bodies? They are inherently
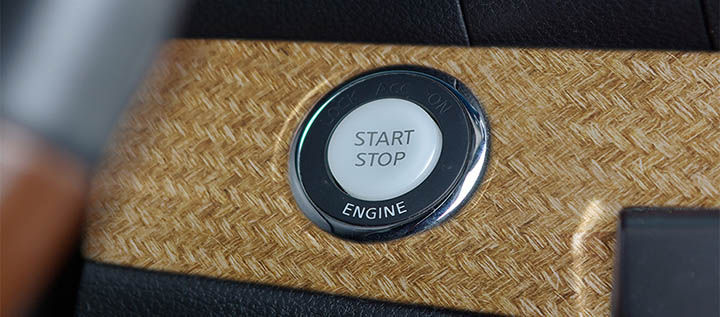
lighter weight on top, so it would seem that the EV industry should want to adopt this very quickly. They can be less expensive than even common fiberglass and have better mechanical properties as well. So, what’s the problem?
Even with these limitations, as you can see from the many pics of trial parts and one-off
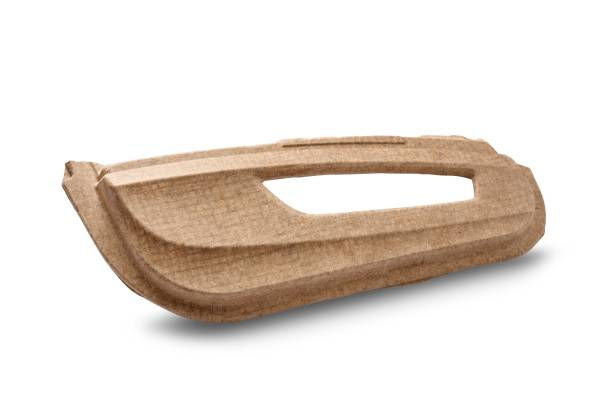
designs, as well as production parts for auto interiors, the overall demand for natural fiber composites is still in its infancy. So, what is being done abut this?
It turns out that lignin – yes the stuff that holds wood together – is an abundant forest product and waste product from making bio-based gasoline and diesel. Since lignin has what is called an “aromatic” structure (groups of Benzene 6-carbon rings all stuck together) it is a natural precursor for carbon fiber. And, it has been estimated that nearly 30% of the organic carbon on earth is lignin. So, there’s lots of this stuff around just waiting to be made into carbon fiber.
The current precursor for carbon fiber that is available on the mass market is a petroleum derived aromatic compound called Polyacrylonitrile or PAN for short. If you recognize the “acrylo” in this you know exactly what this stuff is – it is the basis of fibers for that acrylic sweater you have in your closet. It turns out that lignin has a similar chemical structure to PAN, so it is a natural fit for making carbon fiber. And, since there is so much lignin available in agricultural and forest product waste, it is cheaper than the petroleum based PAN.
There are two companies in Europe that are commercializing processes to do just this – use lignin as a precursor to a carbon fiber instead of PAN. Stora Enso has developed a fiber they call NewFiber® that uses a proprietary process for making their bio-based carbon fiber. They are headquartered in both in Stockholm and in Helsinki. And according to their website they own one of the largest private forests in the world (https://www.storaenso.com/en/about-stora-enso). They pride themselves in being a sustainable materials company whose products by 2050 will be 100% “technically recyclable.”
The second organization is an institution in Germany - Deutsche Institute für Textil- und Faserforschung or DITF – has also created a process for converting lignin to carbon fiber, completely replacing the PAN precursor. In their process, they dry-spin a lignin fiber, and stabilize the fiber at a much lower temperature than what is required for PAN. This lower temperature also allows them to make these fibers at a much faster rate than is currently possible using PAN fibers. Essentially what this does is to make a commercially viable carbon fiber at twice the production rate of current carbon fibers, using a precursor that is significantly lower cost than PAN. This has the potential to lower the cost of carbon fiber to the point that the auto industry can use it for primary structure of their automobiles. In other words, it has the potential to meet the holy grail for carbon fiber composites.
To finish this story on a high note, it appears that even though natural fibers have had a slow rate of adoption – primarily because of some technological hurdles that needed to be crossed. Fortunately, there are processes being commercialized today that will make the sustainable fiber business explode. And this will happen in our lifetimes.
I hope you enjoyed this post. If you can’t tell, this is a subject that I am fairly passionate about as well as being very hopeful about the possibilities that this presents for humanity’s future on this beautiful planet.
Please take a look either on the McFarland Books site to pre-order a copy of my book - https://mcfarlandbooks.com/product/The-String-and-Glue-of-Our-World/. Or you can go to Amazon and see it there as well - https://www.amazon.in/String-Glue-Our-World.
Comentarii